To minimize production disruptions caused by die-casting mold breakdowns, the utilization of long-life SURYODAY core pins is recommended. These critical components, precisely machined and ground from high-quality DIN 1.2344/AISI H-13 steel, are integral to creating holes within die-cast parts. The lifespan of these core pins is further enhanced through processes such as vacuum heat treatment, nitriding, and specialized coatings, contributing to increased operational efficiency and reduced downtime.
Suryoday's Core Pins
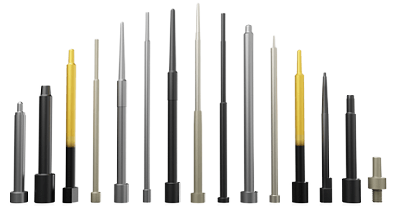
Leading Manufacturer of Core Pins
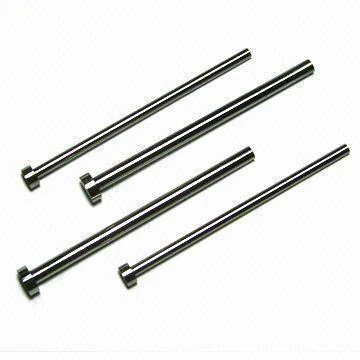
Straight Core Pins
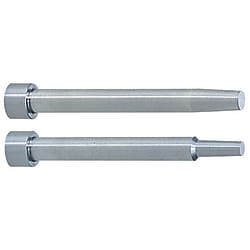
Tapered Core Pin
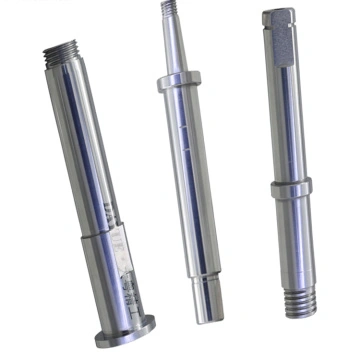
Threaded Core Pins
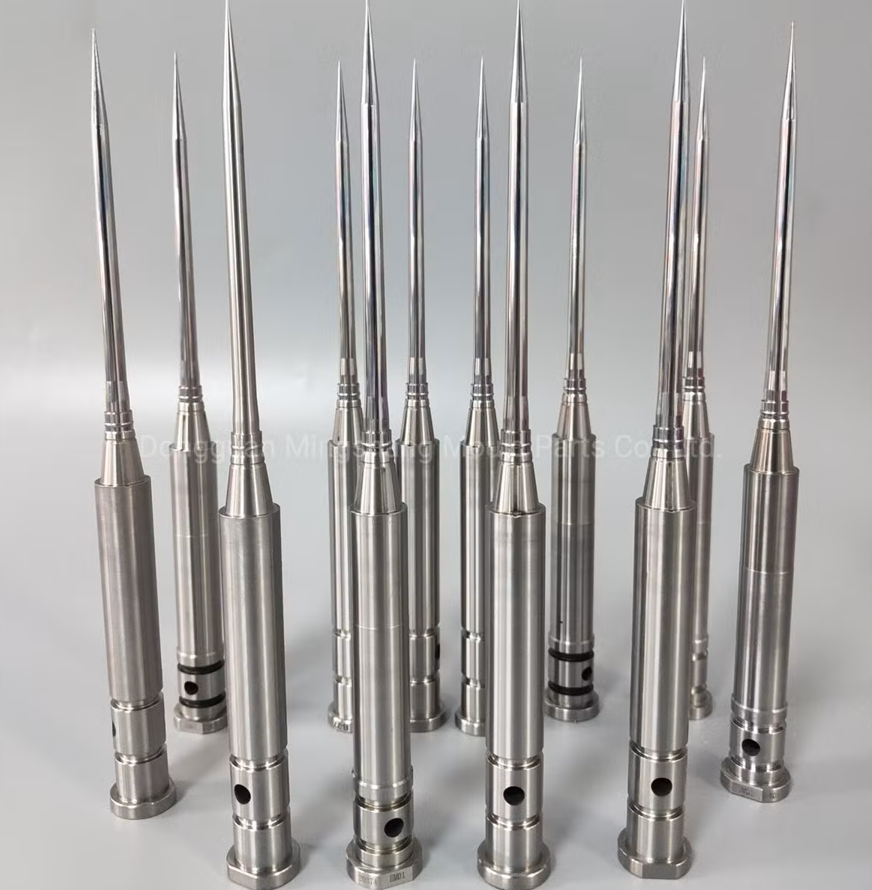
Vented Core Pins
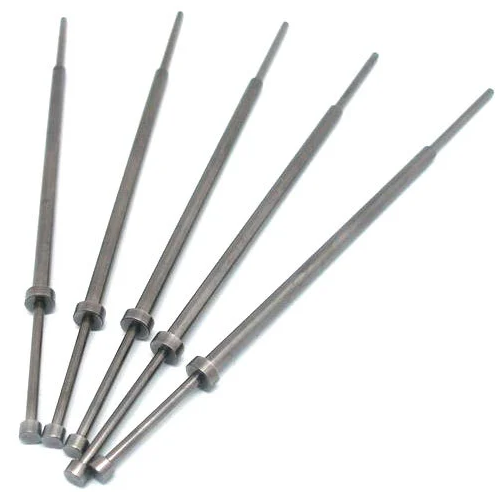
Ejector Core Pins
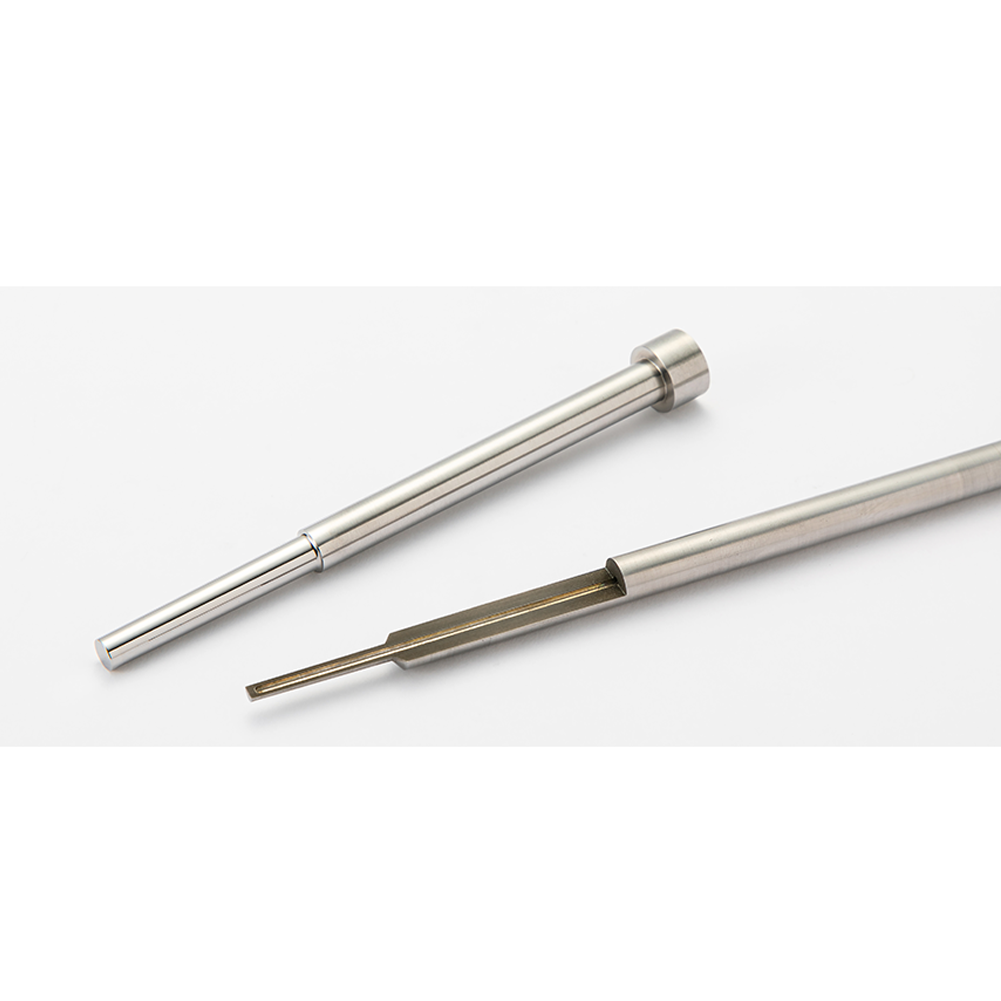
Cooling Core Pins
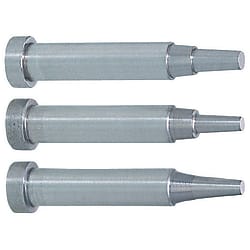
Step Core Pins
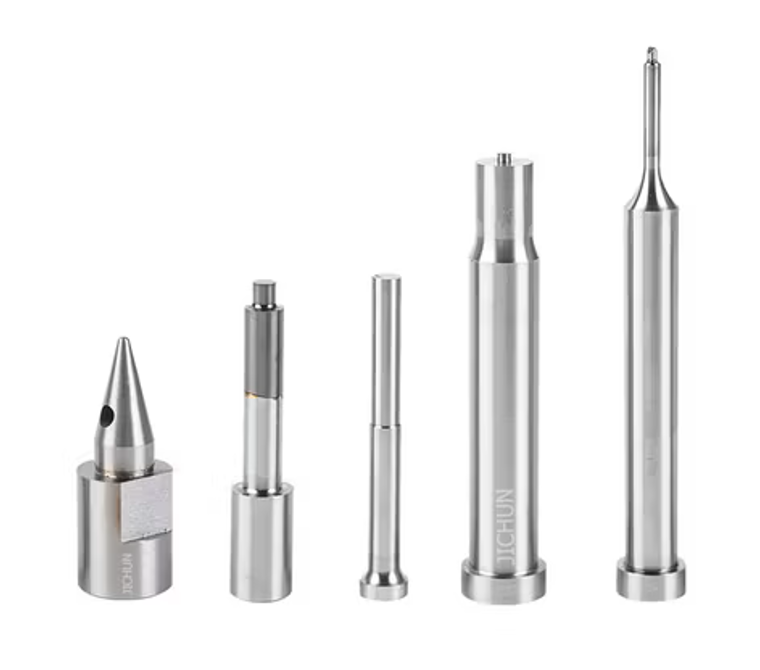
Inlay Core Pin
Die and mold core pins are essential components used in both plastic injection molding and die casting processes to create internal features, cavities, and holes in the molded or cast parts. They come in various types, materials, and with different coatings to suit specific application requirements. Here’s a breakdown of the common types:
Types of Core Pins:
- Straight Core Pins: These are simple cylindrical pins used for creating uniform holes or cavities. They are the most basic and widely used type.
- Tapered Core Pins: These pins feature a slight taper along their length. This design facilitates easier ejection of the molded part by reducing friction and preventing damage.
- Threaded Core Pins: These pins have threads on their surface, allowing for the creation of threaded sections within the plastic or metal components.
- Vented Core Pins: Designed with small air vents or channels, these pins help to eliminate trapped gases within the mold cavity, preventing defects like voids or air pockets in the final product.
- Ejector Core Pins: These serve a dual purpose, acting as both a core pin to form a feature and an ejector pin to push the finished part out of the mold.
- Cooling Core Pins: These specialized pins have internal cooling channels through which a cooling medium (usually water) is circulated. This helps to regulate the temperature of the pin and the surrounding mold area, ensuring uniform cooling of the casting and reducing cycle times.
- Step Core Pins (or Stepped-Type Round Core Pins): These pins have multiple diameters along their length, allowing for the creation of complex internal geometries with varying dimensions.
- Inlay Core Pins: These pins often feature a replaceable tip made of a different material, offering a cost-effective solution for maintenance and allowing for optimized material selection for different wear areas.
- Core Pins for Boss: Specifically designed to create bosses (protruding features with holes) in molded parts.
- Custom/Profile Core Pins: These are precisely machined pins with non-cylindrical shapes to create intricate internal contours and features as required by the part design.
Materials Used for Core Pins:
Core pins are subjected to high temperatures, pressures, and abrasive forces, so the material selection is crucial for their performance and longevity. Common materials include:
- High-Speed Steel (HSS): Offers good wear resistance and toughness, suitable for many general applications.
- Tool Steel (e.g., H13/DIN 1.2344, SKD61): Provides excellent strength, hardness, and heat resistance, making it ideal for die casting and plastic molding. Different grades like Orvar 2, DAC, Orvar Supreme, DAC-S, and Dievar offer specific properties like improved heat check resistance or toughness.
- Carbide: Offers exceptional hardness and wear resistance, making it suitable for high-volume production and abrasive materials.
- Stainless Steel: Provides good corrosion resistance, often used in medical and food-grade applications.
- Beryllium Copper: Exhibits excellent thermal conductivity, which is beneficial for heat-sensitive molding processes and can lead to faster cycle times.
- Copper Alloys (Beryllium-Free): Some manufacturers offer beryllium-free copper alloys as alternatives with enhanced heat transfer rates compared to steel.
Coatings for Core Pins:
Surface coatings are applied to core pins to enhance their properties, such as wear resistance, corrosion resistance, and release characteristics. Common coatings include:
- Nitriding: A surface hardening process that increases wear resistance and reduces the tendency for the molten material to stick to the pin.
- Titanium Nitride (TiN): A hard, wear-resistant coating that also offers good corrosion resistance and lower friction.
- Titanium Carbonitride (TiCN): Offers higher hardness and wear resistance compared to TiN, suitable for more abrasive applications.
- Diamond-Like Carbon (DLC): Provides very low friction and high hardness, improving release and wear life.
- Chrome Plating: Enhances surface hardness and corrosion resistance.
- PVD Coatings (e.g., TiALN, TiCrN): Physical Vapor Deposition coatings offer a range of benefits, including high hardness, wear resistance, and thermal stability, often outperforming conventional coatings in demanding applications.
- Black Oxide/Black Coating: Offers mild corrosion resistance and can improve lubricant retention.
The selection of the appropriate type, material, and coating for a core pin depends on various factors, including the type of material being molded or cast, the complexity of the part design, production volume, operating temperature, and desired part finish and tolerances.